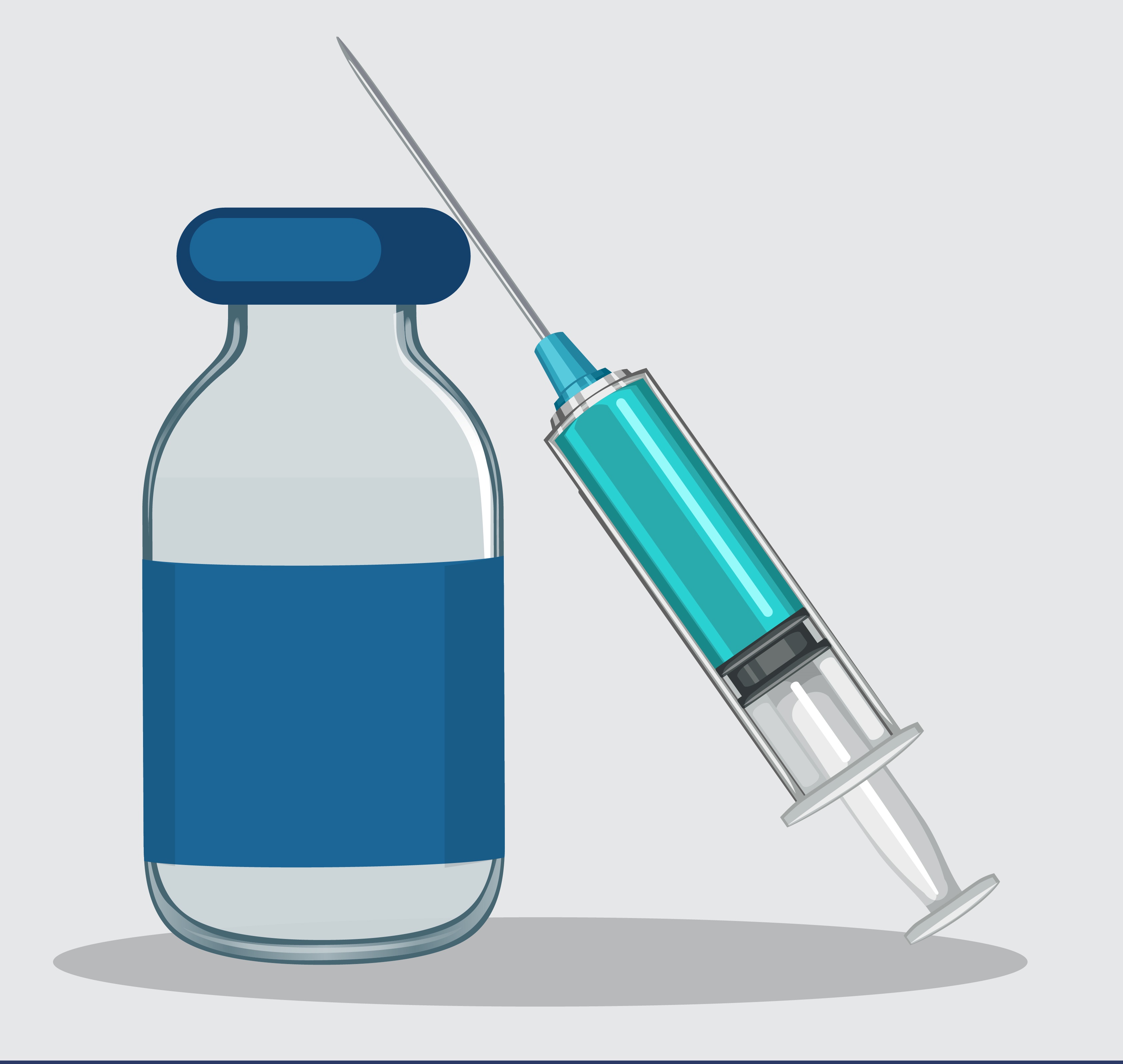
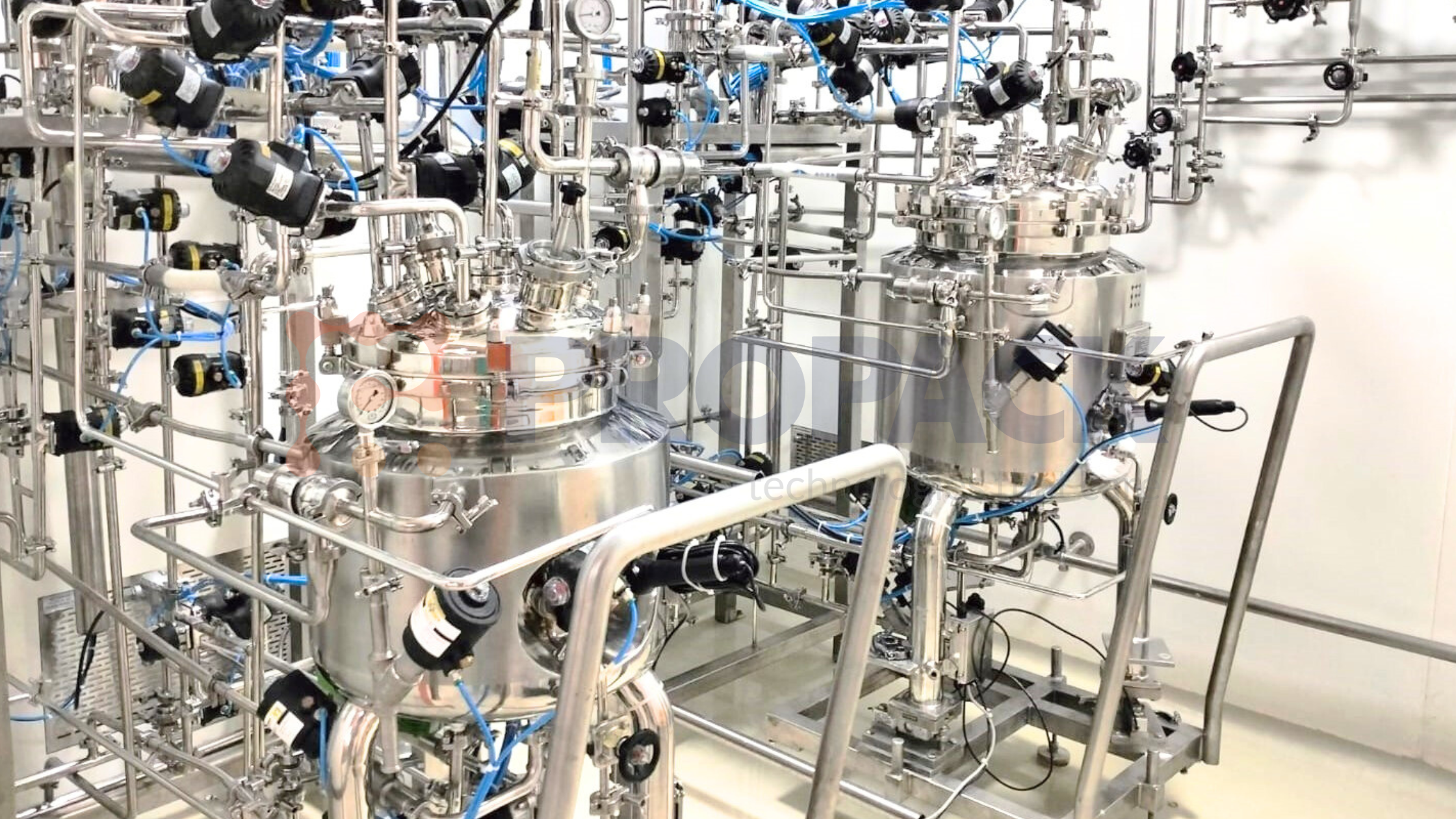
In sterile manufacturing, what doesn’t flow out — grows.
Residual liquid inside a sterile manufacturing vessel becomes a perfect environment for microbial growth. Despite excellent CIP/SIP procedures, if your equipment design doesn’t allow full drainage, contamination risk increases drastically.
Poor drainability:
Real-World Drainability Issues Found in Plants
Here are common design flaws that compromise drainability :
1. Flat or Low-Slope Bottoms
If the tank bottom isn’t properly sloped (>1%), product or cleaning solution can stagnate.
2. Dead Legs in Piping
Improperly designed piping in sterile processing skids creates stagnant zones that cleaning can't reach.
3. Poor Valve Placement
Incorrect placement of flush bottom valves or drain outlets prevents complete evacuation of the product.
4. Weld and Connection Misalignment
Sloppy fabrication or poor welding practice leads to small pockets or “puddling” zones inside sterile mixing vessels. Drainability Standards: What You Should Expect
A trusted sterile system manufacturer must ensure:
What Should Be in a Drainability-Ready Design?
Here’s a checklist a sterile vessel manufacturer should follow :
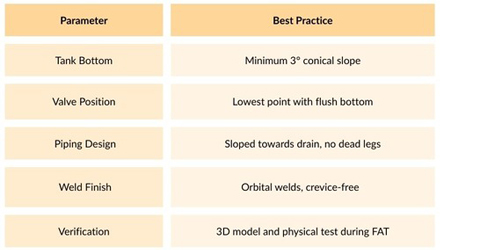
Consequences of Poor Drainability
If this aspect is ignored, the entire sterile manufacturing plant faces risk:
Conclusion
Drainability isn’t just a “nice-to-have.”
It’s non-negotiable in sterile drug manufacturing equipment design.
Choosing an experienced sterile plant manufacturer means choosing equipment that is sterile not just in name, but in performance.
How Propack Technologies Can Help?
At Propack Technologies, we understand the critical role of drainability in sterile processing. As a trusted sterile vessel manufacturer, we engineer every piece of equipment - from sterile manufacturing vessels to complete sterile processing skids with uncompromised design logic, proven drain paths, and complete documentation.
We don’t just meet standards, we build systems that make audits easy, cleaning reliable, and compliance a given.
Looking to upgrade or build your sterile manufacturing plant the right way?
Let’s make it truly sterile.