Ointment Manufacturing Plant
Model : Multi-mix
At Propack Technologies, we provide state-of-the-art ointment manufacturing equipment for producing various semi-solid products such as ointments, creams, shampoo, conditioners, lotion, moisturizers, toothpaste, hair dyes and more. Our automatic ointment cream manufacturing plant can handle capacities from 5 kg to 10,000 kg, with high viscosity and aseptic conditions. We follow cGMP standards for quality and safety.
Our ointment processing systems include fully automated process vessels with optional SCADA package, as well as all the necessary peripherals such as suction pumps, CIP/SIP systems, and transfer pump for filling line interface. We offer customized solutions to meet your specific requirements and expectations.
Benefits of Ointment, Cream, Lotion Manufacturing Plant
- 1Recirculation – short & long loops depending on batch size provided
- 2Contra or Semi-contra agitator for efficient mixing
- 3Variable High Shear processing
- 4Complete CIP & SIP able system with 100% drain
- 5In-house programming expertise to design customized recipe cycles
- 6Automation as per 21 CFR Part 11, PLC / SCADA based automation
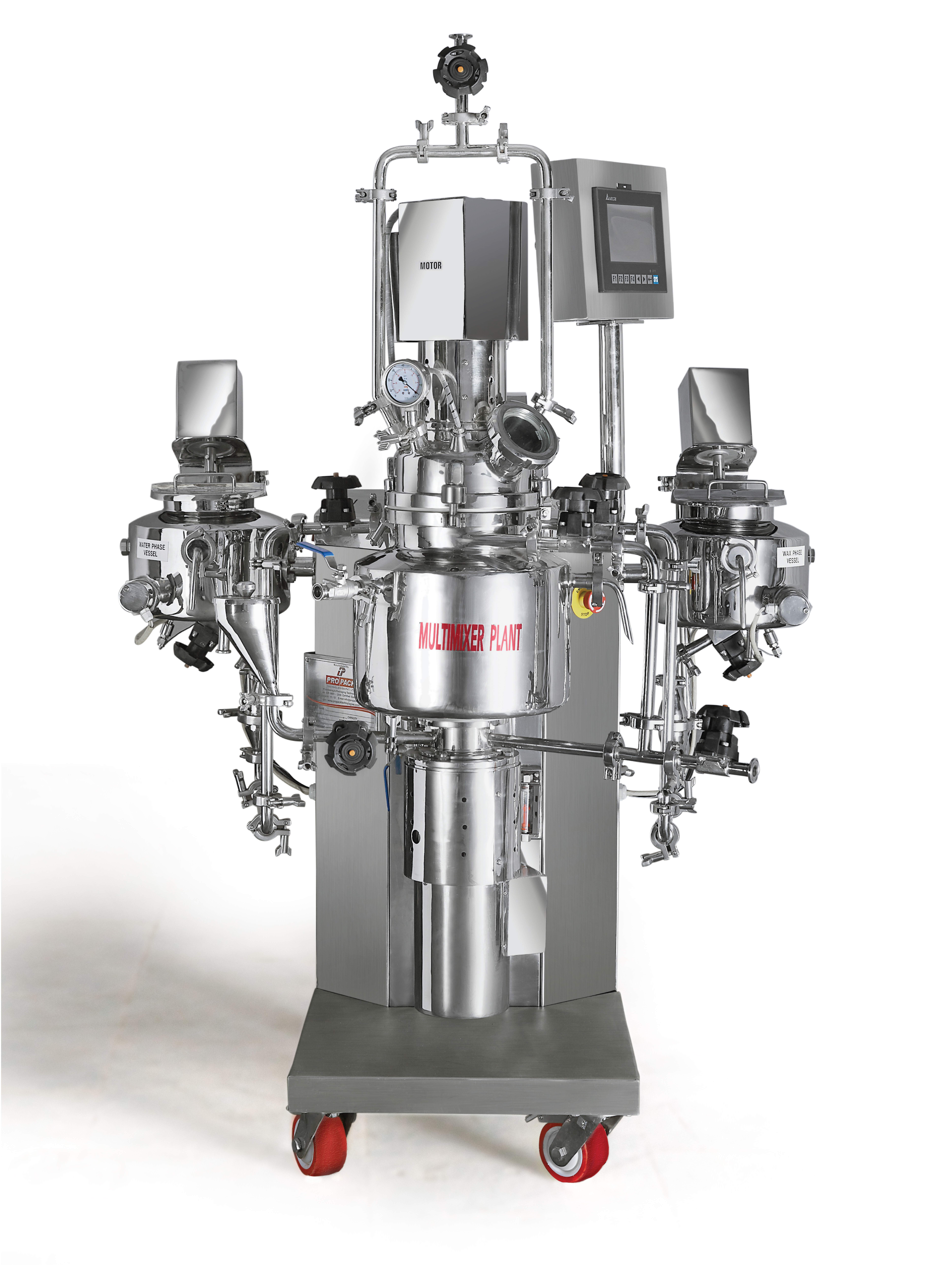
We offer the following customized ointment cream manufacturing plant according to client specific needs,
- Jacketed manufacturing vessel with Anchor type Agitator
- Jacketed wax phase vessel
- Jacketed water phase vessel
- Storage vessel
- Vacuum pump
- Transfer pump
- Meter-in pump for Filling station integration
- Control panel
- Interconnecting pipeline
- Working platform
- CIP and SIP modules
- Automated product transfer
- Automatic Temperature Control with PID
- Load Cells
- SCADA system architecture
Ointment cream manufacturing plant
Propack Technologies is a leading ointment plant manufacturer that provides tailor-made solutions for producing various semi-solid products such as ointments, creams, shampoo, lotion, moisturizers, toothpaste and more. Our automatic ointment cream manufacturing plant comprises of three different phase vessels - a water phase vessel, a wax phase vessel and a main manufacturing vessel - along with other components such as an emulsifier/homogenizer, a vacuum pump, a transfer pump, storage and buffer vessels and a CIP module. All our vessels are made of SS316L grade material and adhere to cGMP guidelines. The plant can be fully automated with pneumatically operated valves for aseptic manufacturing.
Water phase vessel
Water Phase Vessel The water phase vessel is used for mixing all the aqueous phase ingredients with water or a similar solvent. The vessel has a jacket for heating and cooling the solution as per the required temperature, which can be controlled by steam & chilled water or electrical heating arrangement depending on the availability of utilities at the customer’s facility. The vessel has a propeller type stirrer with baffles for uniform mixing and preventing vortex formation. The vessel can suck in the product and the solid ingredients via vacuum suction for minimum contamination. The solid ingredients can be added through an additive hopper at the top of the vessel or a suction port at the bottom of the vessel. After achieving the desired composition, the solution is transferred to the main manufacturing vessel.
Wax phase vessel
Wax Phase Vessel The wax phase vessel is used for mixing all the oil/wax phase ingredients with wax as the main solvent. The vessel has a jacket for heating the wax to improve its solubility at high temperatures, which can be controlled by steam & chilled water or electrical heating arrangement depending on the availability of utilities at the customer’s facility. The vessel has a saw-tooth cutter type stirrer for uniform mixing. The vessel can suck in the product and the solid ingredients via vacuum suction for minimum contamination. After achieving the desired composition, the solution is transferred to the main manufacturing vessel.
Main Ointment Manufacturing vessel
Main Manufacturing Vessel The main manufacturing vessel is used for mixing the contents of the water phase vessel and the wax phase vessel at the appropriate temperature, which can be controlled by steam & chilled water or electrical heating arrangement depending on the availability of utilities at the customer’s facility. The vessel has a top mounted anchor type agitator with teflon scrapers for stirring the product and scraping the material from the walls of the vessel. The vessel also has a homogenizer at the bottom of the vessel for emulsifying the liquid-liquid mixture to a uniform composition. Propack technologies’ homogenizer can reduce the particle size to less than 10 microns. After attaining the desired composition and viscosity of the product, the contents are transferred to a storage vessel through a flush bottom diaphragm valve to minimize product holdup in the tank.
The operations of various pumps, pneumatically operated valves (in case of automated operation) and mixers are carried out through the main control panel. The panel is made of SS304 grade material and has various safety lock systems such as the Emergency stop and Mains supply indicators for safe work and extended component life. The vessels are connected to each other via interconnecting pipelines that are manufactured as per cGMP norms and connected with sealed tri clamp connection.
Our ointment cream manufacturing plant is an ideal ointment making machine that can produce high-quality semi-solid products with minimal human intervention. Our ointment manufacturing machine leverages modern technology and innovation to enhance production performance and efficiency. Our ointment manufacturing equipment is designed to meet the specific needs and expectations of our customers.
Features of Ointment, Cream, Lotion Manufacturing Plant :
- Uniform ingredient dispersion
- No wall caking
- Entire plant operation by one operator and one helper
- Efficient heat transfer in the vessels
- Particle size reduction less than 5 microns
- Reduced batch processing time
- Reduced change over time
- Consistent product composition across different batches
- All contact parts made of SS316L and non-contact parts made of SS304 grade material
- Food grade silicone gaskets
- Vessel design as per ASME guidelines
- Torispherical, Hemispherical and Conical dish top customization availability
- Hydraulic lid lifting arrangement for occasional cleaning
- Static & Dynamic spray ball availability
- VFD for motor rpm controls
- Double cartridge mechanical seal along with cooling arrangement for Homogenizer shaft