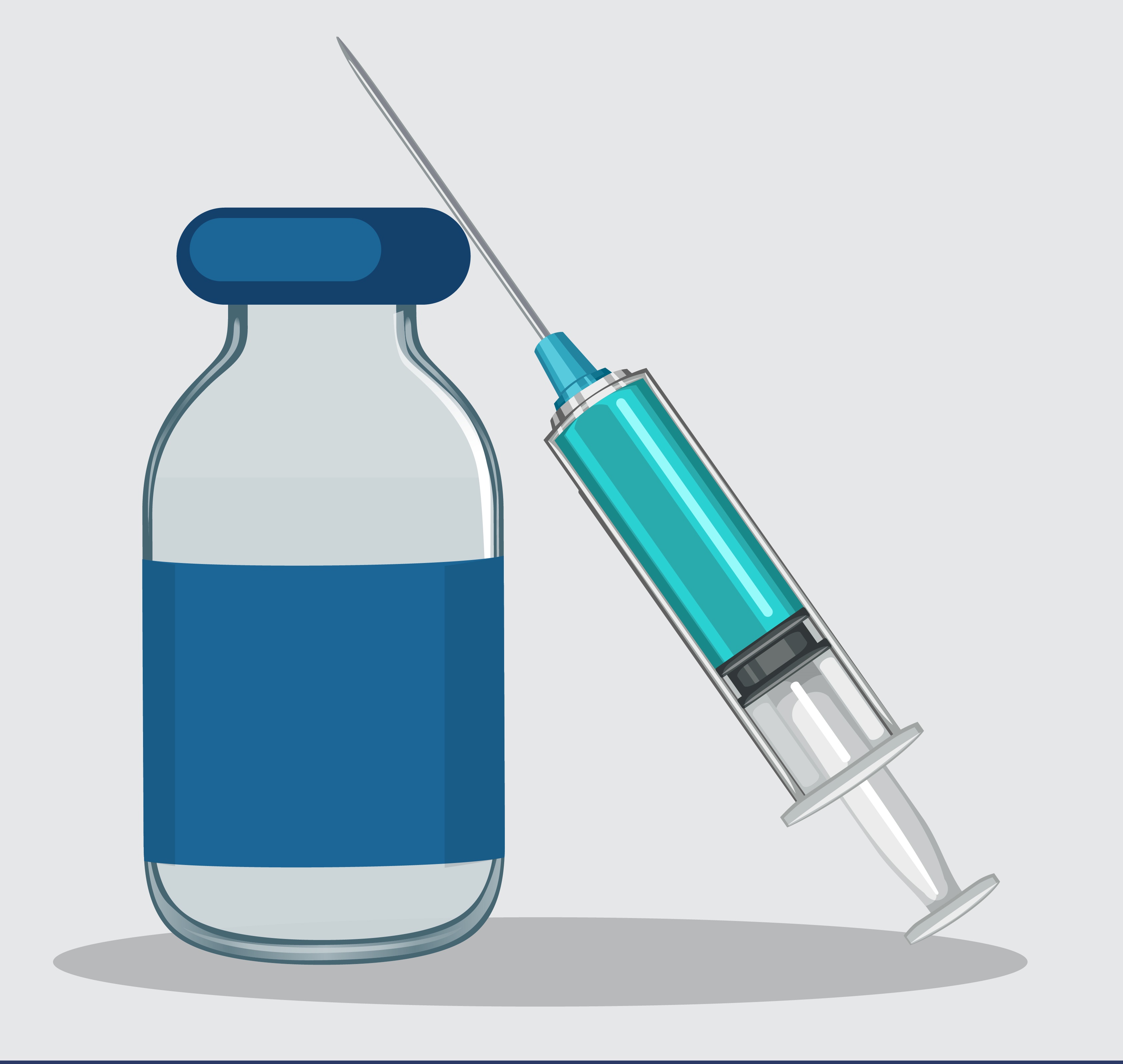
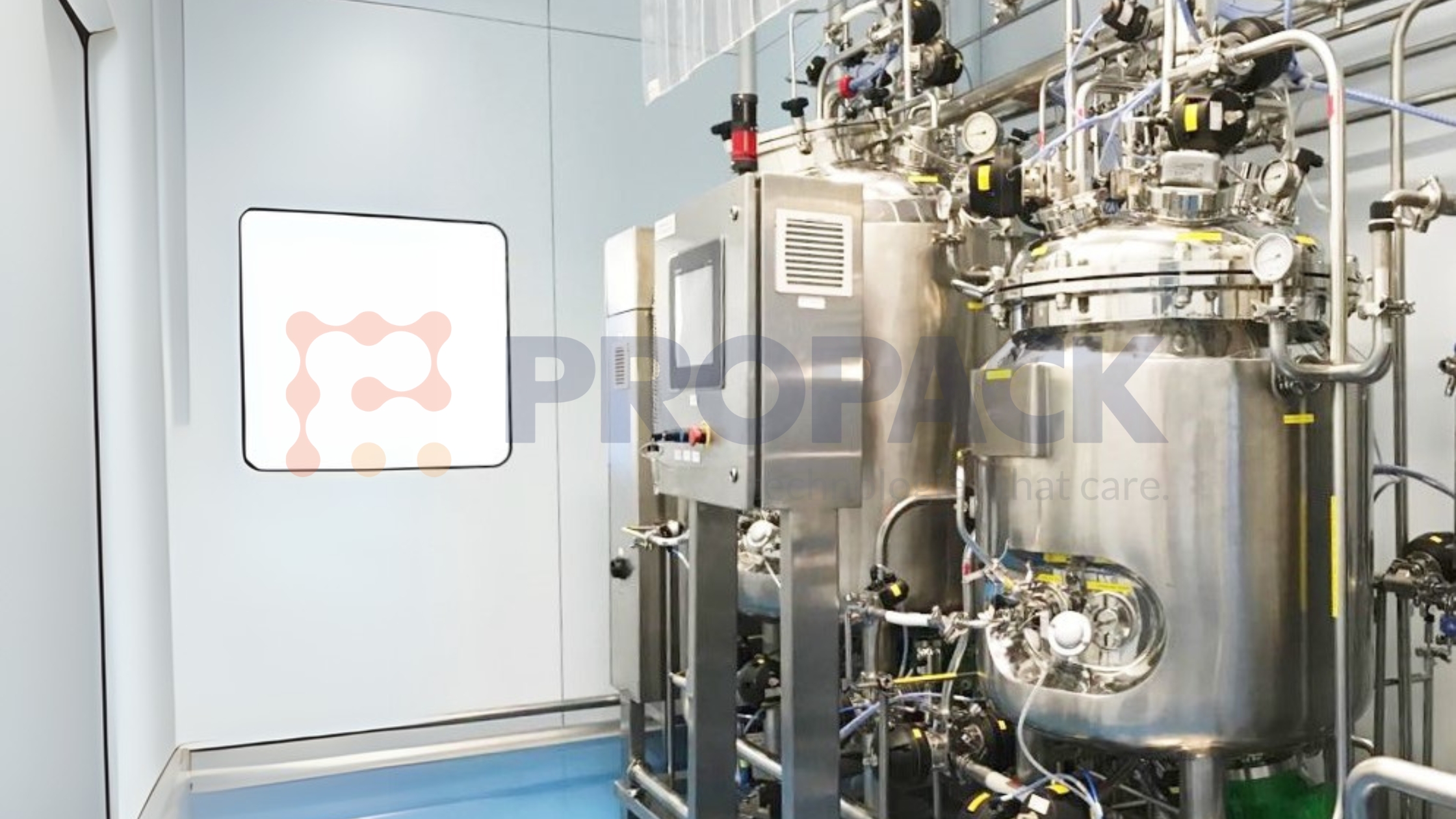
In sterile manufacturing, particularly in the production of injectable and other sterile drugs, the cleaning process is both essential and time-consuming. The Clean-in-Place (CIP) procedure is crucial to maintaining sterility and preventing contamination between batches, but inefficient cleaning designs can increase downtime, reduce productivity, and elevate operating costs.
Fortunately, smart design can significantly improve cleaning efficiency, cutting the cleaning time by up to 40%. This blog will explore how innovative design strategies can optimize your cleaning process, leading to enhanced productivity and faster batch turnovers.
Key Design Features That Cut Cleaning Time
There are several design considerations and features that can dramatically improve CIP efficiency in sterile plants. These include adjustments to equipment geometry, CIP spray ball placement, and valve configurations, among others. Below are the most effective strategies that can reduce cleaning time while maintaining compliance with stringent industry standards.
1. Optimized Tank Geometry for Complete Drainage
Challenge : Flat-bottomed tanks or poorly sloped vessels can create areas where liquids collect, prolonging cleaning time.
Solution : Implementing conical or steep-slope tank bottoms with flush bottom valves allows for faster drainage and minimizes hold-up volumes, reducing the time required for rinsing and drying.
2. Properly Positioned CIP Spray Balls
Challenge : Incorrectly positioned spray devices can lead to incomplete cleaning coverage, forcing longer cleaning cycles and manual intervention.
Solution : CFD-validated spray ball placement ensures thorough cleaning by achieving 360-degree coverage of the entire vessel. For more complex geometries, rotary spray heads can be used to provide better coverage.
3. Eliminating Dead Legs & Crevices
Challenge : The presence of dead legs and crevices in pipes and valves can trap residues and bacteria, requiring additional cleaning cycles.
Solution : Incorporating zero dead-leg valves, orbital welding, and ASME BPE-compliant piping design ensures that your systems are easy to clean, minimizing the need for extra cleaning steps.
4. Smooth, Easy-to-Clean Interior Surfaces
Challenge : Rough or poorly finished tank interiors can accumulate biofilms and other residues, increasing the frequency and intensity of cleaning required.
Solution : Electropolished stainless steel surfaces with a Ra ≤ 0.4 µm finish prevent material buildup and biofilm formation, leading to easier and quicker cleanings.
5. Efficient Drying Systems
Challenge : After cleaning, inefficient drying systems can result in longer drying times, causing delays in production.
Solution : Multi-zone quick-response drying jackets help reduce the drying phase of the cleaning process, ensuring faster turnaround times between batches.
6. Integrated Skid Systems for Automation
Challenge : Manual cleaning connections and complex standalone systems increase the time spent on setup and cleaning.
Solution : Integrated sterile processing skids streamline the cleaning process, reduce human error, and automate the connection and disconnection procedures, enabling quicker and more consistent CIP cycles.
7. Retractable Sensors and Validation Ports
Challenge : The need to remove sensors for cleaning can lead to longer preparation times and the risk of contamination during sensor reinstallation.
Solution : Retractable probes for pH, temperature, and dissolved oxygen (DO) allow for in-situ CIP, reducing the time required to remove and reinstall sensors.
Real-World Impact: A Case Study
One of our clients, a pharmaceutical company involved in sterile injectable production, reported a 40% reduction in CIP time after implementing Propack Technologies’ sterile blending vessels with conical bottoms and optimized spray ball placement. This improvement not only reduced operational costs but also enabled them to increase batch production, improving overall productivity.
What Does This Mean for Your Sterile Plant?
If you are in charge of designing or selecting equipment for a sterile manufacturing plant, consider these design elements carefully. The ability to reduce cleaning time by 40% means :
How Propack Technologies Can Help?
At Propack Technologies, we specialize in designing sterile manufacturing equipment with cleaning efficiency in mind. Our equipment features smart design elements, including fully drainable geometry, optimized spray systems, and compliant piping that enhance cleaning efficiency.
If you are looking to optimize your sterile processing plant for improved CIP efficiency, our experienced team can provide tailored solutions that meet your exact requirements.
Propack Technologies can help you with :
Customized sterile vessels, skids, and blending equipment
Fully compliant CIP designs for fast and efficient cleaning
Documentation and validation support for a seamless integration into your manufacturing process
Discover how we can help you improve cleaning efficiency and reduce downtime in your sterile manufacturing facility.
Get in touch with our team of experts today!