Oral Liquid Plant Manufacturer
Propack Technologies is a leading Oral Plant Manufacturer. Our Liquid processing systems are designed to produce high-quality liquid solutions such as orals, suspensions, cough syrups, drop solutions, expectorants, antacid solutions and more. We can handle capacities from 10 L to 30,000 L, and we follow the cGMP and ASME BPE guidelines for aseptic manufacturing.
We offer a full range of Oral Manufacturing Plant & Machinery and their automation systems with optional SCADA package, suction pumps, CIP/SIP systems, and the filling line interface with transfer pump. Our Orals making Machine is customized to meet your specific needs and requirements.
Benefits of Oral Manufacturing Plant & Machines
- 1Vacuum transfer for sugar
- 2Long bend pipelines to reduce residue in pipelines
- 3Liquid glucose transfer system
- 4Efficient mixing with bottom entry agitator
- 5Inline High Shear mixer for suspension
- 6In-house programming expertise to design customized recipe cycles
- 7Automation as per 21 CFR Part 11, PLC / SCADA based automation
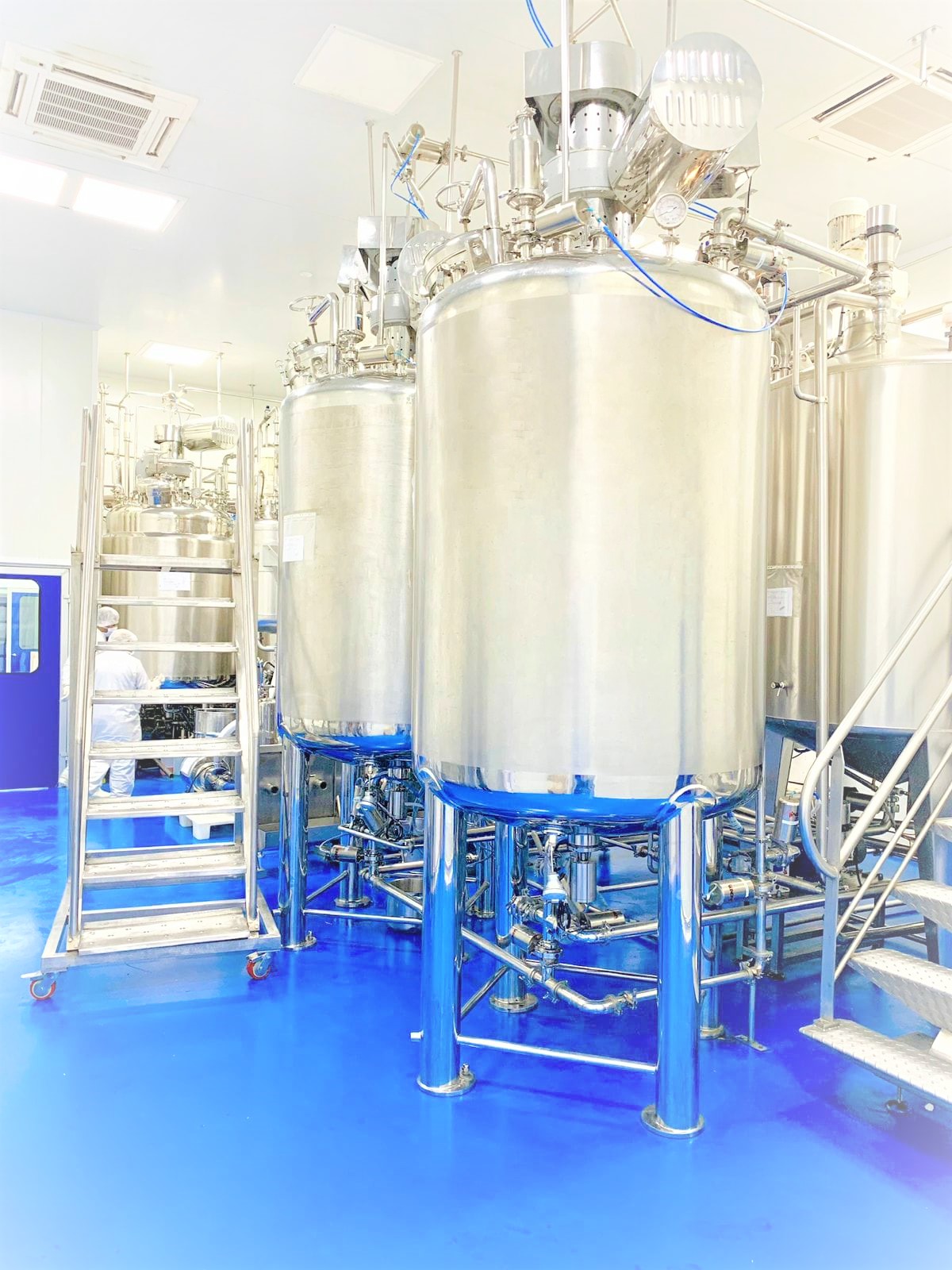
We offer the following customizations according to client specific needs,
- Main manufacturing vessel
- Sugar melting vessel
- Premix vessel
- Sugar discharge bin
- Basket filter
- Zero holdup filter press
- Storage vessel
- Vacuum pump
- Transfer pump
- Metering pump for Filling station integration
- Control panel
- Interconnecting pipeline
- Working platform
- CIP and SIP modules
- Automated product transfer
- Automatic Temperature Control with PID
- Load Cells
- SCADA system architecture
We are a leading Oral Plant Manufacturer in the industry. We offer a range of Oral Mixing Vessels and other components for the production of liquid solutions like syrups, suspensions, and elixirs. Our Oral Plant & Machineries are made of high-quality SS316L grade material and comply with cGMP standards. Our plant can be fully automated with pneumatic valves for aseptic manufacturing.
We are a leading Oral Plant Manufacturer in the industry. We offer a range of Oral Mixing Vessels and other components for the production of liquid solutions like syrups, suspensions, and elixirs. Our Oral Plant & Machineries are made of high-quality SS316L grade material and comply with cGMP standards. Our plant can be fully automated with pneumatic valves for aseptic manufacturingOur Oral Manufacturing Plant & Machineries consist of three different phase vessels – A premix vessel, a sugar melting vessel and a main mixing vessel. The premix vessel is used for mixing the ingredients before adding sugar or glucose. The sugar melting vessel is used for melting sugar and other similar substances. The main mixing vessel is used for blending the contents of the premix and sugar melting vessels at the desired temperature. The plant also includes a sugar charging bin, a basket filter, a zero holdup filter press, an inline homogenizer, a vacuum pump, a transfer pump, storage and buffer vessels and a CIP module.
Sugar Melting vessel
The sugar melting vessel is jacketed for heating and cooling of the solution. The temperature variation can be achieved by steam & chilled water or electrical heating arrangement. A propeller type stirrer and baffles are used for uniform mixing and preventing vortex formation. The product inlet and solid ingredients can be introduced via vacuum suction for minimum contamination. The solid ingredients can be added from the sugar discharging bin via an additive hopper or a suction port. The sugar solution is transferred to the main mixing vessel via the basket filter.
Premix vessel
The premix vessel is used for pre-mixing the ingredients before adding sugar or glucose. This increases the efficiency of mixing. The vessel is jacketed to improve solubility at elevated temperatures. The temperature variation can be achieved by steam & chilled water or electrical heating arrangement. A propeller type stirrer is used for uniform mixing. The product inlet and solid ingredients can be introduced via vacuum suction for minimum contamination. The premix solution is transferred to the main mixing vessel.
Main Manufacturing vessel
The main mixing vessel is used for mixing the contents of the sugar melting vessel and the premix vessel at the appropriate temperature. The vessel is jacketed for heating and cooling of the solution. The temperature variation can be achieved by steam & chilled water or electrical heating arrangement. A bottom mounted propeller type stirrer and an inline homogenizer are used for stirring and grinding the mixture to a uniform composition. The homogenizer reduces the particle size to less than 5 microns. The final product is transferred to a storage vessel through a flush bottom diaphragm valve to minimize product holdup. The product is filtered via a zero-holdup basket filter before dispatching to the filling line.
Features of Oral Manufacturing Plant:
- Uniform ingredient dispersion
- No wall caking
- Entire plant operation by one operator and one helper
- Efficient heat transfer in the vessels
- Particle size reduction less than 5 microns
- Reduced batch processing time
- Reduced change over time
- Consistent product composition across different batches
- All contact parts made of SS316L and non-contact parts made of SS304 grade material
- Food grade silicone gaskets
- Vessel design as per ASME guidelines
- Torispherical, Hemispherical and Conical dish top customization availability
- Hydraulic lid lifting arrangement for occasional cleaning
- Static & Dynamic spray ball availability
- VFD for motor rpm controls
- Double cartridge mechanical seal along with cooling arrangement for Homogenizer shaft